News
Contact Us
General Manager's Office:86-0535-2128130
Customer Service Department:86-0535-2128131
Fax:86-0535-2128129
E-mail:xingjian@ytxingjian.cn
Website:www.ytxingjian.cn
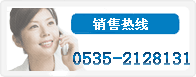
Of grinding on the die life
Mold manufacturing is the continuation of the mold design process to verify the design correctness. Advanced, efficient, high-precision machine tools and automated production technology in the modern mold. Grinding workload will account for 25% to 45% of the total mold manufacturing hours. China's mold industry today has made tremendous progress, but still a big gap with foreign advanced level, see table on the die life. Made a continuation of the mold design process to verify the design correctness. Advanced, efficient, high-precision machine tools and automated production technology in the modern mold. Grinding workload will account for 25% to 45% of the total mold manufacturing hours. China's mold industry today has made tremendous progress, but still a big gap with foreign advanced level, see table on the die life. Mold manufacturing of finished products is closely related to the quality and precision mold manufacturing, in particular, has a close relationship with the accuracy and surface roughness of the surface of the mold cavity.
Actual production, the factors affecting the failure of mold:
① mold structure;
② the mold material;
(3) hot and cold processing manufacturing processes (forging, heat treatment, machining, grinding, EDM, etc.);
④ mold working conditions.
To improve die life, must lead to mold damage causes and factors affecting the careful analysis of the development of methods and measures to overcome.
At present, in the international arena, two mold manufacturing process line:
First, in order to improve the accuracy and quality of machining and EDM, and hand-finishing the workload to a minimum, such as high precision machine tools and high-speed molding milling machine and its process of development, and lay the foundation for the development of this process route.
Second, focus on finishing the polishing and grinding process, the machining time, machining, electrical discharge machining time is almost equal. A mold is made from many parts group with the quality of the parts of a direct impact on the quality of the mold, the final quality of the parts in turn, finishing guarantee.
In most of the mold manufacturing enterprises, the finishing stage of the method used in general grinding, EDM and fitter processing.
Of grinding on the die life did not attract the full attention of the people, due to incorrect grinding process, resulting in the workpiece surface burn, grinding cracks, grinding marks and grinding stress, resulting in the follow-up process and die during servicemechanical fatigue, thermal fatigue crack initiation source, seriously affecting the life of the mold.
Research and explore how to improve the quality of the grinding life of mold, and to extend the service time, and promote mold new technologies, it is the purpose of this paper.
1, the essence of the mold grinding the grinding process is the workpiece to be grinding to a metal surface in the deformation under the action of numerous abrasive moment of extrusion, friction, and then converted to debris and the formation of the smooth surface of the process. The whole process of grinding performance of the role of power and heat.
In the grinding process, the machined surface under the action of cutting heat of thermal expansion, the base metal temperature is lower, so the surface of the thermal compressive stress. When grinding the end, the workpiece surface temperature decreases, the surface has produced a thermal plastic deformation and are subject to the restrictions of the matrix, therefore the surface of the residual tensile stress, the inner layer of residual compressive stress.
② grinding wheel and workpiece arc contact, wheel cutting the workpiece to produce severe plastic deformation and wheel and workpiece frictional resistance formed between the wheel and workpiece size equal to the opposite direction of the grinding force, and because the surfaceplastic deformation within the workpiece material between the metal molecules to produce relative displacement, the formation of internal friction heating, grinding wheel and workpiece, external friction to generate heat, this grinding heat in the grinding zone will produce localized transient up to 1000 ° Chigh temperature, while the wheel is difficult to heat transfer, so 80% of the heat incoming workpiece and the wear debris, and the metal in the solid state transition from a lattice is another lattice with temperature changes, the occurrence of changes in the microstructurefull, in the grinding of hardened steel, cooling the surface layer of the second quenching, part of the retained austenite into martensite, martensite specific volume, specific volume increases, the surface compressive stress, if the millcut cooling is not good, or without coolant surface tempering martensitic transformation occurs, the surface tensile stress (such as γFe into the volume of the iron α-Fe swell 1%), these stress (residual stressup to 500 ~ 1000 MPa), if more than the material yield limit, a grinding cracks, another mold after the heat treatment and quenching did not immediately tempering, quenching temperature is too high, mesh carbonation, tempered and untempered Markovtoo much body or retained austenite, grinding will have a phase transition, so that the stress of the workpiece surface cracks. Grinding crack is a very fine surface cracks, grinding cracks form in general there are three kinds: parallel lines like, network crack-like, eight-shaped crack. The crack direction and shape of the mold about the direction of development of the crack and the grinding wheel in the direction of the workpiece surface grinding, the depth of 0.03 mm.
③ When grinding, the wheel is not sharp, large amount of feed, cool bad-to-peer so that the workpiece surface temperature up to 300 ° C, causing the workpiece surface burn phenomenon.
2, measures to reduce grinding defects
(1) a reasonable choice of the grinding amount of smaller radial feed grinding and even fine grinding. If appropriate, to reduce the radial feed rate and wheel speed, increased axial feed, so that the grinding wheel and workpiece contact area is reduced, the cooling conditions have improved, thus effectively control the surface temperature increased.
② reasonable choice and wheel dressing, white fused alumina grinding wheel, its performance is hard and brittle and easy to produce new cutting edge, so the cutting force is small, less grinding heat to medium-grained granularity. such as 46 ~ 60 mesh better in soft soft (ZR1 's, ZR2 and R1, R2, in the grinding wheel hardness), the coarse-grained, low-hardness of the wheel, self-motivation can be good to reduce the cutting heat. Give priority to the use of the organic binder diamond grinding choosing the right wheel is very important, GD single crystal corundum grinding wheel is more suitable for high vanadium molybdenum steel mold situation, the choice of when processing hard alloy, quenching the high hardness of the material wheel, the wheel of the organic binder from the grinding is good, grind the workpiece roughness up Ra0.2μm recent years, with the application of new materials, CBN (cubic boron nitride) grinding wheels show very good processing effect. CNC forming grinding machines, jig grinders, CNC internal and external circular grinding machine finishing, better than other types of wheels. Timely wheel dressing, keep a sharp grinding wheel grinding, Grinding Wheel slip rub the workpiece surface, extrusion, resulting in the workpiece surface burn, lower intensity.
③ rational use of the coolant, to play three major roles of the cooling, washing, lubrication, and to keep the cooling and lubricating clean, so as to control the grinding heat within the allowable range to prevent the workpiece thermal deformation. To improve the cooling conditions when grinding, such as the use of oil-soaked wheel or the cooling wheel measures. The introduction of the wheel center of the cutting fluid, cutting fluid directly into the grinding zone, to play an effective cooling effect to prevent the workpiece surface burn.
④ the heat treatment after quenching stress decreased to a minimum, because the quenching stress, mesh carbonized organization in the role of the grinding force, the organization phase change easily so that the workpiece cracks. For high-precision mold in order to eliminate the residual stress of grinding, grinding should be carried out low-temperature aging treatment to improve toughness.
⑤The eliminate the grinding stress can also be the mold in the 260 to 315 ° C salt bath and immersed for 1.5 min, then 30 ℃ oil cooling, so that the hardness decreased 1HRC residual stress is reduced by 40% to 65%.
⑥ for precision grinding of the dimensional tolerances within 0.01 mm of precision molds to pay attention to the influence of environmental temperature, require constant temperature grinding. Known by the calculation, 300 mm long pieces of steel, the temperature difference between 3 ° C, the material changes around 10.8μm (10.8 = 1.2 × 3 × 3 100mm deformation of 1.2μm / ° C), all finishing operations are required to fully consider the impact of this factor.
⑦ electrolytic grinding to improve the mold manufacturing precision and surface quality. Electrolytic grinding, the grinding wheel to scrape the oxide film: instead of grinding metal, and thus the grinding force and grinding heat, does not produce the grinding burrs, cracks, burns, and other phenomena, the general surface roughness better than Ra0 .16 μm; In addition, the grinding wheel wear home, such as grinding carbide, silicon carbide grinding wheel wear large about grinding out the carbide weight 400% to 600%, electrolytic grinding, wheel wear and tear is only carbide grinding in addition to the amount of 50% to 100%.
3 Conclusion
Short mold at the time of manufacture to pay full attention to the grinding process, grinding the micro-cracks and residual stress is reduced to a minimum, in order to improve the life of the mold. Mold manufacturing is the continuation of the mold design process to verify the design correctness. Advanced, efficient, high-precision machine tools and automated production technology in the modern mold. Grinding workload will account for 25% to 45% of the total mold manufacturing hours. China's mold industry today has made tremendous progress, but still a big gap with foreign advanced level, see table on the die life. Mold manufacturing of finished products is closely related to the quality and precision mold manufacturing, in particular, has a close relationship with the accuracy and surface roughness of the surface of the mold cavity.